Hyster-Yale
Auto De-Gassing Device for Hydrogen Fuel Cell Cooling System
Hydrogen fuel cells are zero-emission engines that utilize hydrogen and oxygen to create electricity and water. The proton-exchange membrane (PEM) fuel cell stack is composed of repeating layers that are compressed together to create a desired power output. This creates separate sealed channels for hydrogen, air and coolant to flow into and across the stack layers. The cooling system with a fuel cell engine is critical to keep each stack layer at the desired temperature to control the stack water balance (how much water is created from the reaction) and prevent thermal damage to the stack layers. An automatic de-gassing device is a desirable in a fuel cell engine as it will prevent gas buildup within the cooling lines which can cause erratic and reduced cooling flow and damage the fuel cell stack. This student team will work to scope the project, limited to de-gassing device (or system) only, as follows: - The student team will work to utilize a device that shall provide a location for gas in the cooling system to be separated from the coolant and dispersed from the cooling system - The student team will work to utilize a device shall bleed gas without any input from operator or service technician - The student team will work to utilize a device that shall not leak coolant - This student team will work to utilize a device that shall not be made of materials that can leech ions to coolant - Depending on device location, this student team will work to utilize a device that shall be able to function with a cooling pressure between 0.9 (radiator cap release pressure) to 1.3 bar (cooling pump head pressure) - The student team will work to utilize a device that shall function with a coolant flow rate of 35LPM - The student team will work to utilize a device that shall be reasonably sized (think 12oz pop can as max size, but the smaller the better) - The student team will work to utilize a device that does not need to package within the existing B2D1 BBR covers, but should be adaptable to be used with the covers off - The student team will work to utilize a device that can have external hoses that connect to new or existing HYG components if needed This student team will work to achieve the following outcomes: • A patent search. This student team will work to identify existing designs/strategies for de-gassing that exist in industry and need to be part of existing background research • This student team will work to generate CAD models and drawings of prototype • This student team will work to design calculations that went into prototype or testing: -Coolant and gas flow calculations (for device) -Coolant and gas flow analysis (opportunity for CFD?) - Any student driven analysis • This student team will work to conduct the following testing: - Functional testing of device under nominal flow rate and pressure conditions. This will require the creation of a simplified cooling system bench test with the below elements: - Pressurized system (at coolant pressure per device location) - Flowing water at 35LPM flow rate - Ability to introduce known volume of helium into system (as substitute to hydrogen) • This student team will work to produce the following test outputs: - Confirm automatic de-gassing function - Establish if a specific volume of gas is needed before device engages - Confirm device does not leak during function
Faculty Adviser
Aniruddh Vashisth,
Assistant Professor,
Mechanical Engineering
Related News
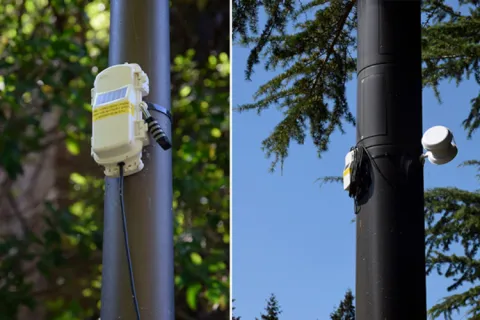
Fri, 09/20/2024 | UW Civil & Environmental Engineering
Smarter irrigation for a greener UW
A new project combines satellite data with ground sensors to conserve water and create a more sustainable campus environment.
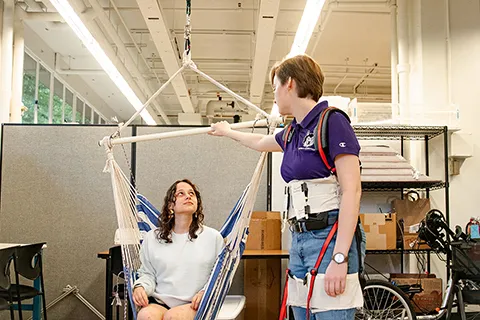
Mon, 09/09/2024 | UW Mechanical Engineering
Testing an in-home mobility system
Through innovative capstone projects, engineering students worked with community members on an adaptable mobility system.
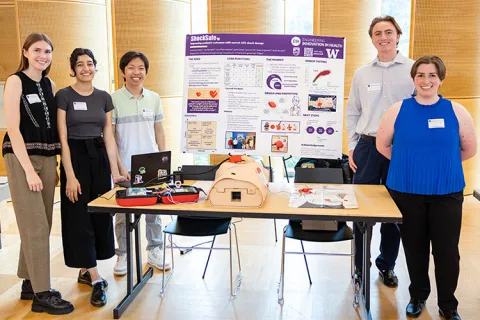
Mon, 08/19/2024 | UW Mechanical Engineering
Students strive to ensure accurate AED shock dosage
ShockSafe, developed by students with the help of mentors from Philips and Engineering Innovation in Health (EIH), can distinguish between children and adults during cardiac arrest emergencies.
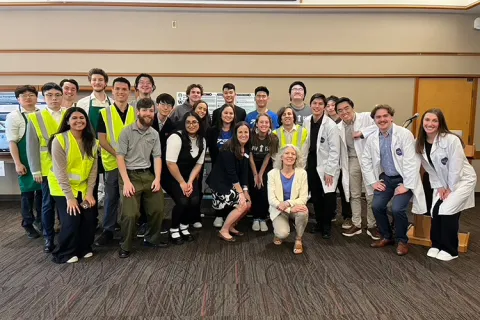
Wed, 08/07/2024 | Snohomish County News
Snohomish County, University of Washington partnership boosts efficiency in enterprise scanning center
UW Industrial and Systems Engineering Capstone Project set to save Snohomish County over $40,000 annually.