Boeing
Composite Part Sectional Repair Housing Apparatus using Expandable Materials
Composite parts require high pressure compaction and heating for curing, which are traditionally achieved using autoclaves. However, the purchase and operation cost of autoclave is significant. In some instances, very large composite parts that have already been cured in an autoclave may require small repairs. Returning the large composite part back into the autoclave is not cost effective and create further delays to the production rate of products such as airplanes. A better method for repairs must be developed; a solution that provides local compaction and heating without the need for another large permanent structure such as autoclave. This student team will work to identify a solution where a localized repair apparatus is sufficient to achieve a capability of holding 100 psi of compaction for one hour and at 350F held constantly. This student team will work to design a system that can conform to and apply compaction pressure and heat to a local surface on a sem-complex large composite part that was previously cured. The system the student team is working to create must be capable of applying 100 psi over a 1 sq-in area and (through model based engineers show how 350F continuous heating can be applied) for one hour. Performance rated on the curing of the repair composite patch that is placed over the original part. The outcome this student is working to achieve is to fabricate a working prototype which will require machined parts, integration of pressure gauges, and proper ergonomic features. Prototype must be able to demonstrate the application of 100 psi on a 1 sq-in precure composite layer that is bonded to a previously cured composite part (coupon will be provided for project by Boeing).
Faculty Adviser
Navid Zobeiry,
Assistant Professor,
Materials Science & Engineering
Students
Anthony Vu
Justin Cabe
Timothy Tien
Tristan Stice
Vy Huynh
Related News
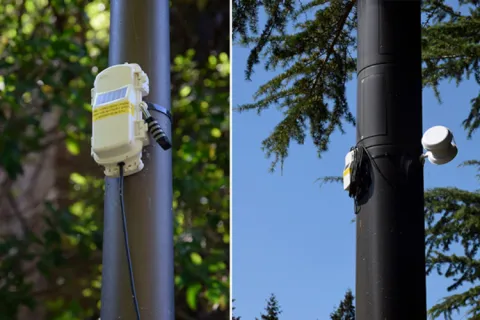
Fri, 09/20/2024 | UW Civil & Environmental Engineering
Smarter irrigation for a greener UW
A new project combines satellite data with ground sensors to conserve water and create a more sustainable campus environment.
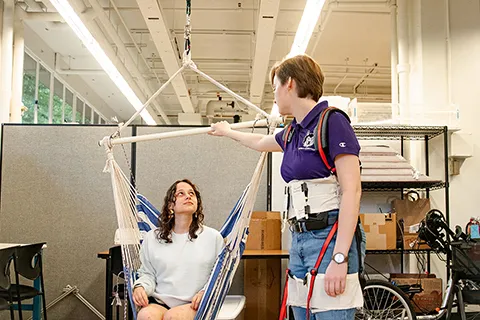
Mon, 09/09/2024 | UW Mechanical Engineering
Testing an in-home mobility system
Through innovative capstone projects, engineering students worked with community members on an adaptable mobility system.
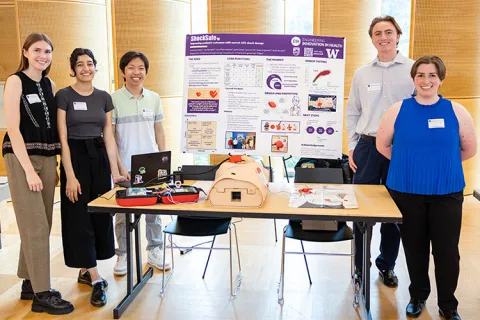
Mon, 08/19/2024 | UW Mechanical Engineering
Students strive to ensure accurate AED shock dosage
ShockSafe, developed by students with the help of mentors from Philips and Engineering Innovation in Health (EIH), can distinguish between children and adults during cardiac arrest emergencies.
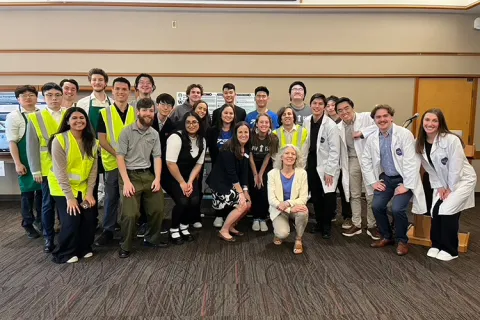
Wed, 08/07/2024 | Snohomish County News
Snohomish County, University of Washington partnership boosts efficiency in enterprise scanning center
UW Industrial and Systems Engineering Capstone Project set to save Snohomish County over $40,000 annually.