Industry-Sponsored Student Capstone Projects
2023/2024
In the 2023/24 academic year, the industry capstone program was supported by 54 sponsors, more than half of which were returning, and 95 real-world projects. Over five hundred fifty students from across the College of Engineering participated. Scroll down to learn more about each project.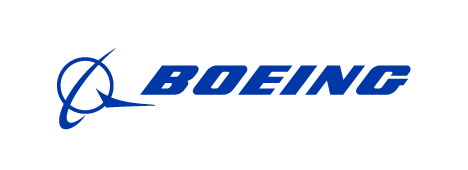
Boeing
737 North Line Wingbox Transportation
The Boeing Company plans to add a new 737 MAX Final Assembly production line within the existing Everett Boeing factory. This new production line is currently named the 737 North Line. The 737 wingbox will continue to be built at the Renton assembly site, and this student team will work to focus on the logistics of the transportation plan for the completed wingbox assembly from Renton to 737 North Line in Everett Washington. The 737 North Line plan requires the completed wingbox to be transported from Renton to Everett via road transportation. These large airplane wing assemblies will need to transported between the two Boeing sites to meet 737 North Line's takt time production requirements. This student team will work to assess and validate the current assumptions for this logistics plan before the 737 North Line starts production in late 2024. The outcomes this student team will work to achieve include: - Create process flow documentation from wing completion in Renton to load in the Everett factory. - Use simulation software to model the transportation plan over different periods of time and traffic conditions. - Provide recommendations on the amount of time it will take to transport the wing from Renton to Everett and what time of day this transportation should occur. Provide similar timing recommendations for recycling the empty trailer back to Renton. - Using simulation results and capacity/capability planning tools, conduct a rate tool analysis and recommend the ideal number of trailers to support this transportation plan for production start-up and various other production rate scenarios. - Create a facility layout design for the ideal wing un-loading area in the Everett factory. - Create a crew utilization plan for overhead crane moves and transportation support as well as crew size recommendation.
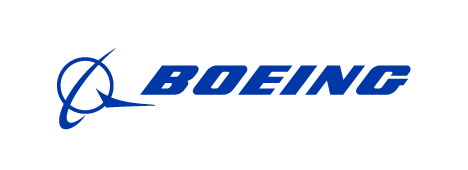
Boeing
AM Machine Gas Flow Characterization & Improvements - Phase 3
Gas flow in metal AM printers is a key process variable. Recirculation and non-uniformity of the gas flow in a printer can be a source of material defects. This student team worked to generate PIV analysis of the baseline gas flow in an EOSM290 printer, and to design devices to improve upon the EOSM290 gas flow test developed by the 2022 & 2023 capstone teams. This student team worked to use CFD to develop easily attachable devices for the EOSM290 AM printer to reduce recirculation and improve gas flow uniformity and generate PIV analysis of the improvements. This student team also worked to analyze materials printed with the improvements and/or different gas flow settings to demonstrate the impact on material properties from gas flow. The student team worked to collect new, targeted Particle Image Velocimetry (PIV) gas flow measurement data to correlate it with existing material performance data (either from UW or provided by Boeing). This student team also worked to build and validate the improvement devices with PIV testing in a mock-up EOSM290 printer developed by prior capstone teams, then worked to build and test materials on the actual UW EOSM290 with these improvement devices to determine if they had an effect on material performance or defect rates.
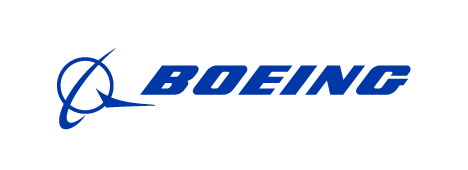
Boeing
Bio-Based Resin Composite Material Testing
The proposed project includes the material testing of a bio-based resin composite. This bio-based resin is made from the byproduct of sugarcane waste production and is being investigated for its sustainability benefits and flammability performance. Material testing will include GC-MS (gas chromatography mass spectrometry) to evaluate resin constituents. Other thermophysical evaluation like DSC and TGA are desired. The project will also include understanding material chemical sensitivity with testing and evaluation. The composite system will be composed of reinforcing fibers, either glass or carbon, with a bio-based thermosetting polymer matrix. All work will include an appropriate test plan to evaluate resin constituents and chemical sensitivity. Deliverables will include evaluation, photos, and reports of all tests done on materials.
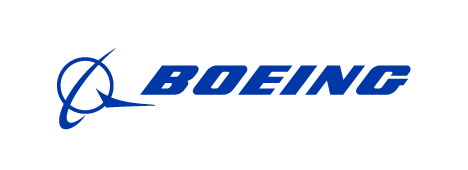
Boeing
Boeing Regional Commercial Aircraft Design & Wind Tunnel Testing
The smaller regional airplane market currently has products that are based upon older designs that have their origins in the late 1980’s and early 1990’s. The Boeing 2022 Commercial Market Outlook (CMO) forecasts a 2,120-unit regional aircraft over the next 20 years. This presents an opportunity to develop new regional aircraft to satisfy the 75-seat portion of the market that meets the US domestic “Scope Clause” that has significantly better fuel burn and economics than existing options. The overall goal is to be at least 20% better than existing 75 seat regional jets in 500 nmi block fuel per seat with a cost to build that is comparable to the existing aircraft. This airplane should be designed to be competitive with the Mitsubishi SpaceJet M100 (76 seats), the Bombardier CRJ700/900, the Comac ARJ21-700 and De Havilland Canada Dash 8 Q400. This student team worked to achieve the following two goals: 1) Create the preliminary design of the airplane, including integration and sizing 2) Conduct model-scaled wind tunnel testing and compare against analytical predictions This student team worked to: • determine the aircraft size and propulsion system to meet the required mission (75 seat, 1500nmi range, 6000ft Take-off field requirement, cruise Mach 0.75-0.78), … (see RFP for details) • optimize the payload arrangement to allow for ergonomic passenger comfort • create a design that considered environmental impacts by using Sustainable Aviation Fuel (SAF), minimized emissions, and was sensitive to noise pollution (quiet). • minimize production cost by choosing materials and manufacturing methods appropriate for the annual production rate that was supported by the team’s assessment of the potential market size. • make the aircraft visually appealing so it is marketable and identified what features are important to the operators for different missions. • make the aircraft reliability equal or better than that of comparable aircraft. • make the aircraft maintenance equal or better than that of comparable aircraft. The project outcome this student team worked to achieve is the preliminary design of an aircraft that meets the requirements and is validated through limited testing. The deliverables this student team worked to achieve include: • a technical report that presents the design of the aircraft clearly and concisely, and that includes all relevant aspects, pertinent analyses, and studies supporting design choices. (Details of the required report content can be found in the RFP) • a scale wind-tunnel model • experimental results from the wind-tunnel test
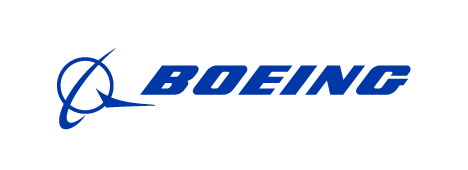
Boeing
Coatings for Improved UV protection of Additively Manufactured Photopolymers
This student team will have the opportunity to apply their classroom knowledge to a real world problem with no predetermined “right answer”. Through this project, students will have the opportunity to work to execute this ambitious project and will gain insights on what it is like to work at a company like Boeing. About the project: Additive Manufacturing (AM) is revolutionizing the way we fabricate aerospace components by enabling increasingly complex part designs. The Photopolymer 3D printing process has many advantages including the ability to print small complex parts with excellent surface finish. Historically the use of photopolymers in aerospace production have been limited by poor elevated temperature mechanical properties, flammability, and susceptibility to UV degradation. Recent advances in photopolymer materials have improved temperature resistance and flammability, but the material remain susceptible to degradation when exposed to ultraviolet light (UV). This student team will work to focus on evaluating and improving coating technologies to shield photopolymer parts from UV light. The students will work toward this project objective by selecting coating materials, modifying them with pigments/additives to improve their UV protective properties, and by studying the effect of coating thickness on UV protection on additivity manufactured photopolymers. This student team will work to use testing to determine the degree of UV protection offered by each coating system. This student team will work to: -Select a set of existing coating materials and additives/pigments with the potential to improve the coating's UV protective properties -Develop test plan to study the effect of coating thickness and the addition of additives/pigments on the coating's UV protective properties on additively manufactured photopolymers. -Modify coatings with selected additives/pigments -Paint and test photopolymer samples printed at Boeing according to the test plan
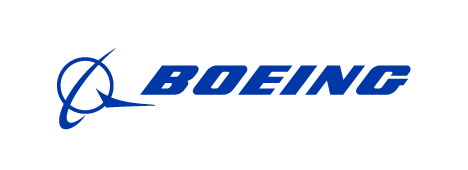
Boeing
Composite Part Sectional Repair Housing Apparatus using Expandable Materials
Composite parts require high pressure compaction and heating for curing, which are traditionally achieved using autoclaves. However, the purchase and operation cost of autoclave is significant. In some instances, very large composite parts that have already been cured in an autoclave may require small repairs. Returning the large composite part back into the autoclave is not cost effective and create further delays to the production rate of products such as airplanes. A better method for repairs must be developed; a solution that provides local compaction and heating without the need for another large permanent structure such as autoclave. This student team will work to identify a solution where a localized repair apparatus is sufficient to achieve a capability of holding 100 psi of compaction for one hour and at 350F held constantly. This student team will work to design a system that can conform to and apply compaction pressure and heat to a local surface on a sem-complex large composite part that was previously cured. The system the student team is working to create must be capable of applying 100 psi over a 1 sq-in area and (through model based engineers show how 350F continuous heating can be applied) for one hour. Performance rated on the curing of the repair composite patch that is placed over the original part. The outcome this student is working to achieve is to fabricate a working prototype which will require machined parts, integration of pressure gauges, and proper ergonomic features. Prototype must be able to demonstrate the application of 100 psi on a 1 sq-in precure composite layer that is bonded to a previously cured composite part (coupon will be provided for project by Boeing).
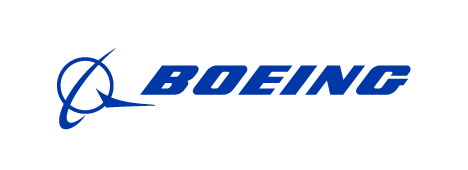
Boeing
Composite Stop Beam Design
This student team was provided with a generic/non-proprietary stop fitting shape representing one end of a passenger entry door stop beam. The student team was asked to create 3 stop beams using different composite manufacturing methods, which could include hand layup, chopped fiber, oriented fiber tows, 3D printed continuous carbon fibers, resin transfer molding, or similar. This student team was tasked with comparing the composite parts to an aluminum baseline part (that they fabricate). This student team worked to explore novel fabrication techniques for stop fittings and to compare fabrication techniques to better understand the strengths and weaknesses of the fabrication techniques. This student team worked to test each part to failure and compare their results. The student team worked to provide a test report detailing their findings of which composite manufacturing technology provided the strongest stop beam element. The student team worked to compare the stop beam to an aluminum baseline part and to describe the pros and cons of each material system.
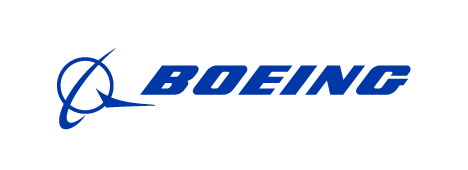
Boeing
Effect of Bondline Thickness on Mechanical Performance of Adhesive Bonds
Adhesive bonding systems consist of four critical elements: substrate material, adhesive material, surface preparation, and bonding/cure process. The adhesive bond performance is optimal within a thickness range, dependent on the specific adhesive and cure process. There is growing interest in understanding the effect of varying the bondline thickness of film (or paste) adhesives on mechanical performance to determine appropriate bondline thickness limits. In addition, there is interest in understanding which adhesive bond performance test methods are useful for assessing bondline thickness effects. This student team will work toward two objectives: (1) determine an appropriate bonding system with given substrate and film or paste adhesive composite materials and (2) characterize mechanical performance dependence on bondline thickness. To meet these objectives, this student team will work to: 1. Propose a suitable secondary bonding system cure process and surface preparation for given substrate and adhesive composite materials, ensuring bonding system achieves cohesive failure within adhesive. 2. Propose a suitable method for controlling bondline thickness within bonding system. 3. Propose an appropriate test plan/DOE plan for typical structural tests of adhesive bond performance. Design and develop test coupons with varying bondline thickness for comparison. 4. Perform mechanical tests. Characterize variable bondline thickness with respect to mechanical performance. 5. Publish results of tests - conclusions and recommendations. This student team will work to create a technical summary report on findings of testing.
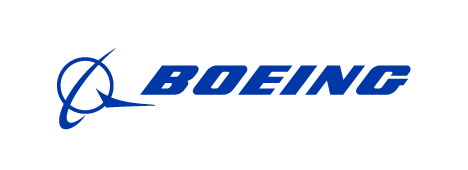
Boeing
Evaluation of Plasma Treatment Detection Methods for Thermoplastic Substrates
Atmospheric plasma has been shown to activate inert bonding surfaces, such as thermoplastic substrates. Structural repair of thermoplastic substrates requires specific plasma treatment parameters to be employed - power, number of passes, speed of a pass, and stand-off distance between substrate and the plasma source. To the naked eye, a machined thermoplastic composite surface that is plasma treated appears no different from one that is not treated. This creates a challenge confirming whether the surface was adequately treated or not. There exist potential detection methods for determining whether plasma treatment was adequately performed. This student team will work to identify potential non-contact and contact methods to detect plasma treatment and then characterize the effect of those methods, such as potentially contaminating the surface, on bond quality. To achieve this objective, this student team will work to identify and evaluate the relative effects of plasma detection methods on bond quality of machined thermoplastic (TP) substrates, by performing the following: 1. Literature survey and selection of non-contact and contact methods for detecting plasma surface treatment. 2. Design of Experiments (DoE) methodology to establish the optimum test matrix - evaluate effectiveness of detection method(s) and the effect of the detection method(s) on bond quality 3. Perform Double Cantilever Beam (DCB) testing per ASTM D5528 (Mode 1 Interlaminar Fracture Toughness test) **Obtain or fabricate substrate test coupons using carbon reinforced thermoplastic (TP) materials **Obtain or fabricate repair test coupons using carbon reinforced thermoset material **Plasma Treat TP coupons per standard approved treatment parameters (to be provided by Boeing) using robot or mechanical fixture controlled plasma heads. **Subject some plasma treated TP coupons to plasma detection method(s) **Apply mitigation techniques to remove any potential contamination **Bond DCB coupons (TP coupons bonded to thermoset coupons) per standard process using adhesive and perform DCB tests 4. Document test report Boeing designs capstone projects to be multi-disciplinary, encouraging engagement of students with diverse backgrounds and use of universal design principles. Mentors will offer students opportunities to expand their skill set beyond university education. Boeing is a global corporation and these projects enable maturation of technologies that benefit our diverse global market.
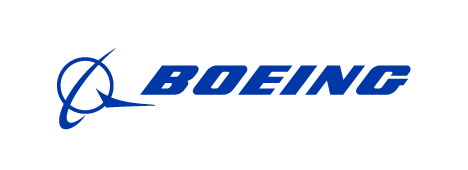
Boeing
Formula Motor Sports Car Improved Part Design, Material and Fabrication Techniques
This student team worked to identify an application that would improve performance, improve quality, lower cost, and/or a shorten lead time for parts on a formula style race car. To accomplish this, this student team worked to learn about different materials, processes and fabrication techniques applied to parts designed for a formula style race car, and select the optimal materials to design the part(s) with. The student team also worked to define testing requirements, build the part(s) for installation, and analyzed and tested (as needed) on the formula style race car to validate that the part(s) was/were suitable for use on the car and for design optimization. The student team also worked to finalize the design and load/strength requirements and refine the current design to ensure it would function properly and was safe for use on the race car. Finally, the student team worked to complete a report documenting the analysis and design building and testing process and results.
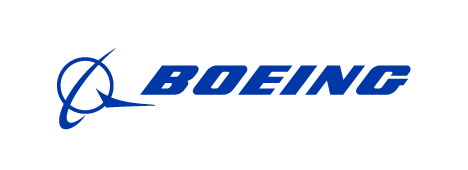
Boeing
Laser Surface Smoothing Optimization
Laser processing of substrates is an evolving technology that offers advantages in processing rate, sustainability and ergonomics. As laser capabilities ramp up, the characterization of more material systems is required to expand the scope of opportunities. This student team will work to evaluate the effectiveness of lasers to remove material from a polymeric surface to yield a smooth, uniform surface, as an alternative to sanding. (Sanding is used to smooth surfaces for many end-item applications, ranging from decorative laminates, to decorative paint finishes.) To date, the laser has been used to remove a given amount of a material, but follows the contour of the underlying surface. The objective this student team will work to accomplish is to determine the effectiveness of laser processing for near surface ablation and smoothing of material in terms of rate and uniformity. The materials this student team could potentially use can be either 3D printed (FDM) materials with characteristic, repeated surface roughness from the resolution of the layer height or other relevant polymer based composite systems. First, the student team will work to analyze the untreated surface for surface topography and surface energy analysis. The student team will also work to design a laser ablation test to determine the effectiveness of the laser to remove material. Third, the student team will work to develop a rate of removal program that can be tuned to the topology of the surface. And then, the student team will work to tune the laser program to smooth the surface to a consistent profile. Following this, the student team will work to characterize the material for the effectiveness at smoothing the surface. The questions this student team will work to answer include: what are the material properties of the exposed substrate? When comparing the surface energy and adhesive properties of the material to the control specimens, what is the effect of too little power and too much power delivered? This student team could work to test on various grades of materials (such as high temperature thermoplastics like PEEK or PEKK or Onyx, common low-grade polymers like ABS or PLA or ASA, bagside composite, etc.). The student team will work to develop laser delivery settings that are appropriate for each class of materials for surface smoothing. The student team will work to record the test results of the of the methods performed. Provide a report out of the approach, techniques attempted, results and conclusions. Last, the student team will work to provide a future work statement based upon the conclusions drawn.
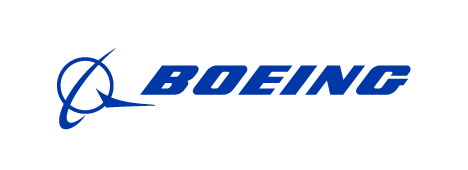
Boeing
Light - Quantum Emitter Interaction Modeling
This student team worked to analyze the fundamentals of light interaction with a quantum emitter in support of quantum sensing, communication and electronics control design concepts under consideration at Boeing. The students worked to define, model and solve increasingly complex and physically accurate quantum mechanical systems relevant to these technological areas. The Project Mentor provided initial models and propose solution methodologies, and the students worked to seek alternative methods and additional topics of interest to apply to problem solving. Motivations of this project were to: (1) advance existing and (2) seek alternative modeling and solution methods to apply to Boeing's quantum projects; (3) encourage potential future Boeing employees to develop quantum technological, mathematical and computational skills. This student team began the project with analysis of the Jaynes-Cummings model, which in its simplest form describes the interaction of a single photon mode (plane wave) with a two-energy level quantum emitter (such as an atom). One example of interest to Boeing was Photon Addition, where an excited emitter transitions from its higher energy level to lower energy level while interacting with an incident "signal" photon, thus emitting an additional photon that may carry some of the characteristics of the incident photon, thus amplifying the signal, improving its detection and measure, and increasing its signal-to-noise ratio in a quasi-noiseless manner surpassing classical statistics. The quantum system would then be incrementally expanded to include multiple photon modes interacting with one or more physically realizable emitters with multiple energy level transitions. As later stage of the project, the student team worked to expand to interaction with entangled photons and analysis and solution of the Master's Equation, which describes the aforementioned light-emitter interaction as well as interaction with the environment and inclusion of even more physical realism of the quantum emitter characteristics and performance, relevant to existing or potential quantum emitters under development. Examples of quantum emitters that the student team considered to be physically characterized in the models include: trapped atoms, solid state emitters such as Nitrogen vacancy centers and hexagonal Boron Nitride, and quantum dots. The student team worked to develop analytical and numerical techniques to efficiently solve these systems, and worked to evaluate performance of the models through simulation of physical measurements as they relate to examination of spontaneous vs. stimulated emission, increase in signal-to-noise ratio, and amplification of information encoded in the photon signal (such as polarization, phase, etc.) A desired outcome this student team worked toward was to develop efficient numerical methodologies to model and evaluate the performance of light-emitter interaction design concepts. The student team worked to use the models, with increasingly complex systems of multiple photon modes and multiple energy level emitters, to compare and differentiate various quantum emitter systems and evaluate their performance in increasing the sensitivity of photon signal detection and measurement, increasing range and resolution of quantum imaging systems, evaluating quantum communication concepts. The student team worked to deliver reports and presentations of the incrementally complex light-matter interaction models and their solutions, analytical and numerical algorithms for solving the models, and suggestions for future advancement of these techniques that could lead to additional research projects.
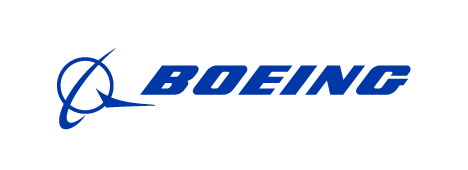
Boeing
Natural Fiber Composites
This student team will work to fabricate natural fiber composite systems from a down-selected polymer matrix with an appropriate test plan to evaluate mechanical performance. The composite system will be composed of reinforcing fibers sourced from plant matter or renewable material with a polymer matrix of either thermoplastic or thermoset polymer. Each panel will be fabricated in a similar process with option to adjust process for optimization. Panel and coupon fabrication will be accompanied by an appropriate test plan to evaluate mechanical performance and compare to existing fiber-reinforced plastic (FRP) composite systems. This student team will work to include evaluation and comparison of handling materials during panel fabrication, defect formation in cured panels, ease of coupon fabrication, and mechanical properties data for use of potentially less environmentally impactful materials due to the renewable nature of the fiber sources. Students with knowledge on composite fabrication (to help with making the materials needed to be tested) and with interests in performing mechanical tests and interpreting results are encouraged to apply.
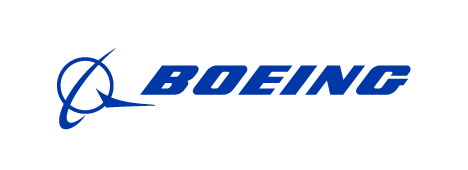
Boeing
Sustainable Airport Operations
A number of international and regional airlines have started to utilize zero emission vehicles (ZEV) as part of their ground support operations. Numerous technical, logistic, and financial challenges have prevented the widespread adoption across the breath of airports and airlines. This student team will work to create a plan to utilize zero emission vehicles (ZEV) for ground support equipment for an airline at a local commercial airport (i.e. Seattle-Tacoma, Paine Field, Spokane, etc.). This student team will work to apply their knowledge of sustainable transportation, traffic optimization, and infrastructure to identify and mitigate challenges for sustainable airport ground operations. This student team will work to create a final report that will serve as a guide for implementation. This student team will work to provide a final deliverable detailing the utilization plan, risks, and estimated Ozone reduction. The student team should work to include in their report discussions about methods, assumptions, conclusions, and areas for further consideration. This student team will work to provide a final deliverable including the details of the utilization plan, risks, and estimated Ozone reduction. This student team will work to define the vehicles needed to support airline ground operations and the infrastructure needed to support both conventional and zero emission vehicles (ZEV) for comparison - scalable for size. ZEVs can be electric, hydrogen, or a combination. Other details the student team will work to take into consideration (although not limited to the following) include: charge/refuel times, ZEV mileage, availability rate and time.
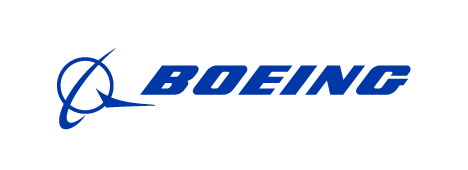
Boeing
Sustainable Surface Layer Removal to Enable Recycling
Usage of carbon fiber composites in airplanes improves product sustainability by increasing durability, reducing weight, enabling part life extension, and improving producibility. However, the disposal of end-of-service composites has emerged as a pressing environmental challenge. While there are methods to recycle the carbon fiber reinforced polymer material by itself, current technology gaps prevent recycling feasibility of the end-of-service mixed material. One of the challenges hindering the effectiveness of recycling processes is the presence of surface layers, such as coatings and adhesives. This student team will work to conduct research, identify potentially efficient methods, and experiment with those methods (time and lab resources permitting) for the removal of process-limiting surface layers during end-of-life carbon fiber recycling. The objectives this student team will work to accomplish include: identifying and exploring innovative techniques that can safely and efficiently remove these surface layers, enabling enhanced recycling efficiency and promoting sustainable practices. Additionally, this student team will work to identify potential use cases for the byproducts generated from surface layer removal, thus promoting the circular economy. The outcomes this student team is working toward will potentially contribute to enhanced recycling efficiency, sustainability, and overall reduction of the environmental impact associated with end-of-life carbon fiber composites. This student team will work to address the following research questions: 1. What are the different types of surface layers commonly found on end-of-life carbon fiber composites? 2. How could these surface layers impact the efficiency of existing carbon fiber recycling processes? 3. What are the existing methods and techniques used for removal of similar finishes and surface layers during production, maintenance or other recycling industries? 4. Can novel approaches be developed or adapted from question 3 to improve the efficiency and effectiveness of surface layer removal? 5. How can the removed surface layers be properly handled, reused, recycled, or safely disposed? Methodology: 1) This student team will work to conduct a literature review and available case study Analysis. The student team will work to conduct an extensive review of existing literature and research papers to gather insights into the types and characteristics of surface layers, their impact on recycling, and existing removal methods. Additionally, this student team will work to review case studies of existing recycling facilities to gather real-world data on the effectiveness of current surface layer removal techniques. 2) This student team will work to collect expert interviews and surveys. This student team will work to interview industry experts and stakeholders internal to Boeing and throughout supply chain collecting insights and inputs to further advise characterization, process availability, existing removal methods, etc. This student team will also work to design and administer surveys to gather data from industry experts, researchers, and recycling practitioners to understand their experiences, challenges, and insights related to surface layer removal in [carbon fiber or related] recycling. 3. This student team will work to generate a research report. This student team will work to provide a summarized research report of the literature review, case studies, expert interviews and surveys. 4. This student team will work to provide experimental analysis. This student team will work to develop and execute a series of experiments to evaluate the efficiency of different removal techniques, potentially including but not limited to mechanical, chemical, and thermal methods, for identified types of surface layers. This student team will also work to collect and characterize outputs including gases and solid byproducts. 5. This student team will work to provide comparative analysis and sustainability considerations. This student team will work to analyze the results of the experiments, comparing the effectiveness, efficiency, and environmental impact of the different removal techniques. This student team will also work to propose possible alternative use cases for byproduct materials. 6. This student team will work to provide an experimental Report. Based on experimental findings the student team will work to achieve, this student team will work to identify methods most viable and compatible with end of service carbon fiber recycling. Propose potential modifications or improvements to existing techniques or opportunistic novel approaches for efficient surface layer removal. This student team will work to provide a report of all testing and findings. Desired outcomes this student team should work to accomplish include: 1. Identification and characterization of the common types of surface layers present on end-of-life carbon fiber composites. 2. Evaluation of the impact of surface layers on the efficiency of the carbon fiber recycling process. 3. Comparison of existing removal techniques and their effectiveness for different types of surface layers. 4. Recommendation of adapted optimized or novel methods for efficient removal of process limiting surface layers. Identify byproducts 5. Characterize the removed surface layer byproducts and provide recommendations of their potential use cases or sustainable and safe disposal. 6. Two reports – midterm research summary and final experimental summary detailed above.
Related News
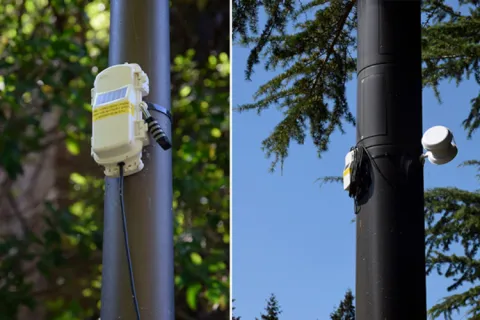
Fri, 09/20/2024 | UW Civil & Environmental Engineering
Smarter irrigation for a greener UW
A new project combines satellite data with ground sensors to conserve water and create a more sustainable campus environment.
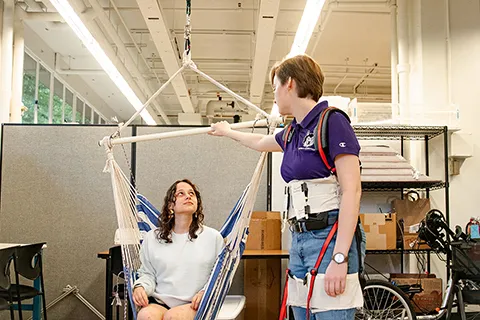
Mon, 09/09/2024 | UW Mechanical Engineering
Testing an in-home mobility system
Through innovative capstone projects, engineering students worked with community members on an adaptable mobility system.
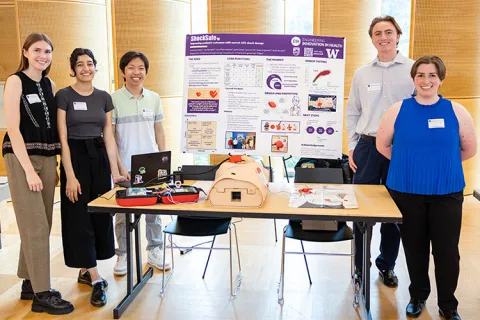
Mon, 08/19/2024 | UW Mechanical Engineering
Students strive to ensure accurate AED shock dosage
ShockSafe, developed by students with the help of mentors from Philips and Engineering Innovation in Health (EIH), can distinguish between children and adults during cardiac arrest emergencies.
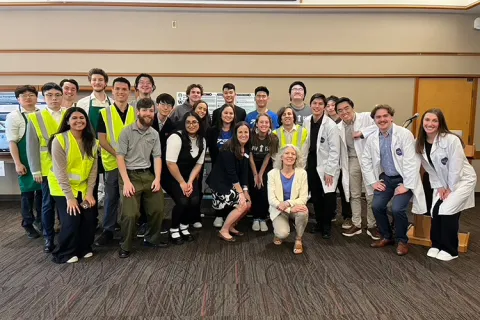
Wed, 08/07/2024 | Snohomish County News
Snohomish County, University of Washington partnership boosts efficiency in enterprise scanning center
UW Industrial and Systems Engineering Capstone Project set to save Snohomish County over $40,000 annually.