Industry-Sponsored Student Capstone Projects
2022/2023
In the 2022/23 academic year the industry capstone program was supported by 56 sponsors and 99 real-world projects. Nearly five hundred and fifty students from across the College of Engineering participated. Scroll down to learn more about each project.
PACCAR
State of Health Analysis for LFP Battery Second Life
BEV batteries still have some usable life once they are at vehicle end of life. These electric batteries see battery degradation typically due to exposure to high temperature, rapid charge and discharge cycles, and repeated utilization of maximum storage potential of the battery over time. This student team sought to understand the battery degradation over time along with the historical performance behavior of the battery, as this would help PACCAR to understand the battery second life repurposes. This student team attempted to analyze battery State of Health (SOH) through the vehicle life cycle and propose its future for its 2nd life once the batteries are at end of life for the vehicle use. The outcome this student team worked towards was an analysis report to complete a SOH analysis on the battery at the end-of-vehicle life stage through end-of-life stage.

PACCAR
Validated Material Model with Damage
Paccar Technical Center currently does not have validated material model with damage. With limited requirements for crash/impact analysis in truck industry and a focus more towards durability analysis, there was no urgent need for material model validation with damage associated with it. However, with Paccar's development on the Battery electric vehicle and the requirement associated with impact analysis, the need for validated material model with failure has become utmost importance in order to provide good prediction on impact scenarios. This student team worked to create a test set-up for casting material (maybe one of PACCAR's casting components) with failure (coupon testing) to gather all the relevant data for material model development. This student team also worked to develop the material model with damage created, verified, and validated by test data.
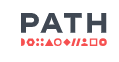
PATH
Mobile Emergency Care System
Approximately 2.7 million people are bitten by venomous snakes annually, leading to 138,000 deaths globally. Victims are generally poor subsistence farmers in rural communities of low- and middle-income countries (LMICs), and for every death there are 3-5 victims who survive but are permanently disfigured or disabled. Given that snakebite envenomings occur predominately in rural areas and the window for care is limited, it becomes incumbent upon the victim to travel to the nearest care facility as fast as possible. In these environments, though, the travel time to a care facility is often measured in hours. This tyranny of distance also holds true for other life-threatening conditions that the world's rural poor face. In rare instances a few communities have developed ambulance or ambulance-like networks, but resource constraints often mean that these are little more than just vehicles to transport patients, with no ability to stabilize or deliver care en-route. This student team worked to design a mobile emergency care system should incorporate the minimum required devices for ground ambulances found in high-resource settings. This was able to include but was not limited to a laryngeal mask-airway system/ventilator, suction circuit, syringe driver/infusion pump, and suite of vital sign monitoring tools (pulse oximeter, thermometer, sphygmomanometer or equivalents). Potential broader scope could have included an AED. It was aimed to support both adult and pediatric use. Conversations with clinicians/EMS personnel helped inform a target product profile.
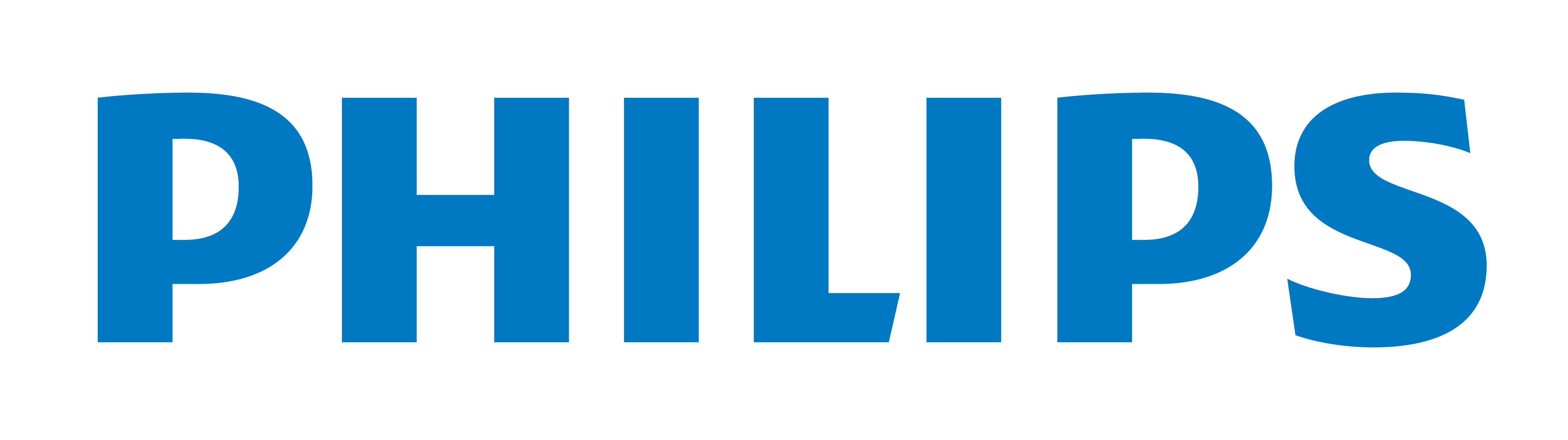
Philips
Quantification of the Usage/Life Counter for Cables/Paddles
There are many detachable cables used by EMS and hospitals for patient care. These cables are reusable and so can be used frequently or rarely depending on the situation. Two examples are ECG leads and internal/external defibrillation paddles. Hospitals and EMS systems do not currently have a good way of tracking the age and wear on cables and companies cannot easily set warranty coverage. This project aimed to develop creative methods to track the reuse and reprocessing cycles (cleaning) without relying on user interaction (logs, etc.).
Puget Sound Restoration Fund (PSRF)
Seaweed Solutions: Harnessing Wind and Sun for Drying Nuisance Seaweed
Intertidal shellfish operations in Puget Sound can be burdened by seaweed that accumulates on cultivation gear throughout the growing season, oftentimes suffocating clams, oysters and other farmed shellfish. These seaweeds grow quickly and abundantly during warm months, fueled by nutrients from upland sources, the ocean, and nutrients excreted by the shellfish themselves. While seaweeds absorb carbon and nitrogen and initially provide food and habitat for marine organisms, they also decompose, releasing the nutrients back into the environment. This can then contribute to the degradation of local water quality and threaten the livelihoods of many shellfish growers in Puget Sound. PSRF, in partnership with three shellfish growing operations, is leading a two-year pilot project to develop experimental removal systems and market pathways for the excess seaweed that accumulates on and in aquaculture gear at the participating shellfish farms. Wet seaweed is heavy and immediately begins to decompose once removed from the salt water, so an important part of the project the students worked towards is extending the “shelf life” of seaweed and enabling its use in burgeoning seaweed-based markets. Some growers have established relationships with local organic farmers that can most often receive the seaweed as soon as it is harvested, while others aim to stockpile a biomass for new markets. Transport, however, of wet seaweed is incredibly labor intensive and time sensitive. This student team worked to look for ways and/or systems to eliminate the time sensitivity and labor associated with transporting wet seaweed by reducing the weight (and moisture content) and jump-starting the oxygenation process of the seaweed on site to reduce noxious/unpleasant odors. This student team also worked to develop a passive drying system in order to produce a lightweight, easily transported seaweed biomass product. While solving a here-and-now problem for growers, this student team also worked to help recycle seaweed into sustainable pathways and be integral to the potential for renewing sea-to-land nutrient flows in response to actions identified by the Blue Ribbon Panel to help mitigate Ocean Acidification, (a product of climate change) in Puget Sound. Desired outcomes of this project included this student team working to deliver a schematic drawing of the full proposed system and working to develop a physical prototype of the proposed system (full or partial).
Seagen
Infrastructure System Ownership
Seagen has a need to have a full understanding of the infrastructure systems that support their R&D and manufacturing facilities. The industry model for this to assign infrastructure systems to engineers within the Real Estate and Facilities (REF) Engineering Center of Excellence (COE). These engineers would be responsible for understanding their assigned systems. Seagen currently does not have this program developed and implemented. This has been due to limited time and resources. Seagen has extensive experience on how to establish and maintain a program like this. This student team worked to develop this program alongside Seagen’s REF Engineering COE experienced engineering staff. With Seagen engineers, this student team worked to develop a project charter, system priorities, determine which data to collect, provide data analytics direction for the monthly status meetings, and deliverables. Infrastructure systems are assigned to facilities engineers. This student team worked to: 1. Develop a charter 2. Develop building and infrastructure system priority – We will use building B8 on the North Creek (NC) site the pilot project to work through the process before taking on all sites and buildings. NC will be the manufacturing facility to implement the program after the pilot project is completed and lessons learned have been implemented into the program documentation. 3. Develop a priority of the systems to address in phases 4. Document the design basis of each system 5. Document the current available capacity for the infrastructure systems 6. Review each system for reliability risks 7. Identify future projects to mitigate the risks in item 4. 8. Propose an agreed upon frequency of review 9. Propose the format of review, KPIs to monitor, data analytics approach, BPI dashboard, etc. Anticipated outcomes this student team worked to generate include system documents that summarize: 1. Basis of design 2. Current operating parameters 3.Reliability and Risk analyses 4. Summary document for presentation to others 5. Dashboard that summarizes all the above items per system
Related News
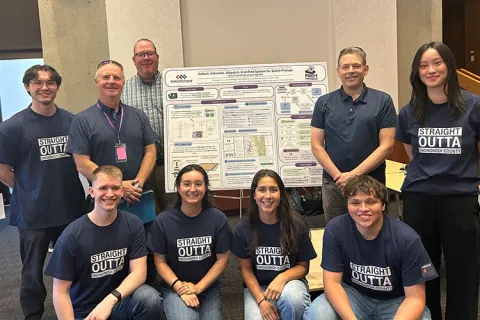
Thu, 07/17/2025
UW engineering students develop smart ballot solution
UW engineering students develop smart technology solution to improve ballot collection for Snohomish County.
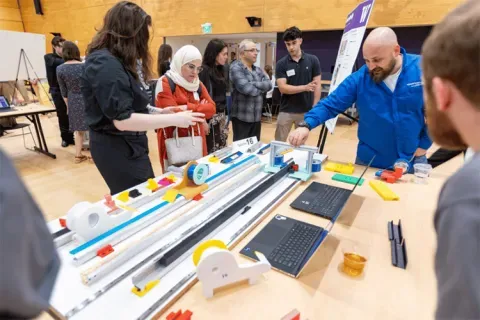
Mon, 07/07/2025 | UW Mechanical Engineering
Capstone creations
Students displayed innovative capstone design projects at the 2025 expo.
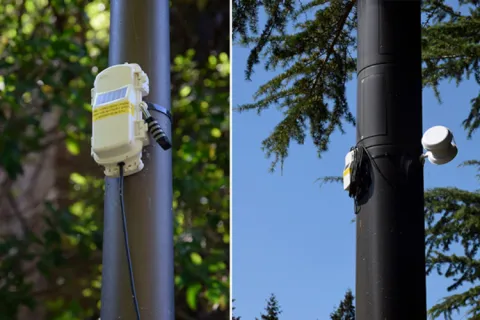
Fri, 09/20/2024 | UW Civil & Environmental Engineering
Smarter irrigation for a greener UW
A new project combines satellite data with ground sensors to conserve water and create a more sustainable campus environment.
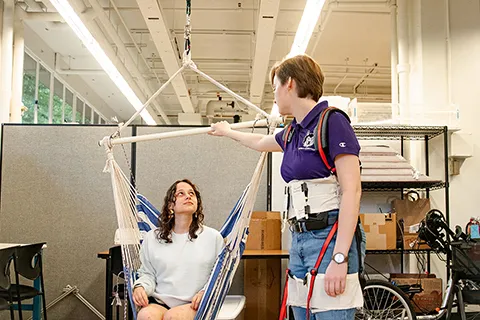
Mon, 09/09/2024 | UW Mechanical Engineering
Testing an in-home mobility system
Through innovative capstone projects, engineering students worked with community members on an adaptable mobility system.