Industry-Sponsored Student Capstone Projects
2022/2023
In the 2022/23 academic year the industry capstone program was supported by 56 sponsors and 99 real-world projects. Nearly five hundred and fifty students from across the College of Engineering participated. Scroll down to learn more about each project.Access Laser
An Optoelectronic Closed-Loop Control System for RF Amplifiers
This student team worked to design and implement a closed-loop control system that detects presence of an optical signal and monitors Voltage Standing Wave Ratio (VSWR) during the plasma initiation inside a laser. The generated control signals were intended to be used to appropriately control the Radio Frequency (RF) Amplifier driving the laser. The team worked to create a system control, including an optical detector module and a in-line VSWR detector module. Through this project, students set out to learn about RF circuits, PCB design, electronic component selection, design for EMC, and design for manufacturability among other topics.
Access Laser
Optimizing Inventory/WIP Management to Reduce NonValue Added Inventory Processing Time
Access Laser Company has identified a couple of concerns with the management of inventory in the build area: Issue 1: They spend X hours of labor kitting per part - NVA (non value add time) Issue 2: They have quality issues including misspicks, misskits, running out of inventory, damaged parts, etc. Issue 3: They have additional NVA time as in-between work steps as lasers have no standard area so they spend time organizing and hunting for parts/wip This student team worked to analyze and suggest modifications to Access Laser's layout, inventory management style, and/or work design that minimize NVA when it comes to processing WIP and inventory. The student team also worked to consider quality improvement and a process to mitigate work stoppage due to running out of material, and to accomplish tangible improvement of Cycle Time. The student team also sought to create a WIP visualization and status board to easily identify where a laser is at any given time.
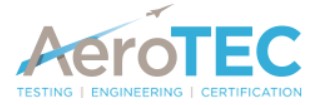
AeroTEC
UAV Flight Test Development
The purpose of this project was for the student team to attempt to develop a program and capabilities that will allow future students to test designs in a controlled environment using industry standard best practices. Referring to work completed in past Aeronautics and Astronautics capstone projects, this student team worked to identify two of the most well-developed supersonic and highly efficient structural aircraft for additional research and development in the areas of modeling, simulation, data acquisition and telemetry systems. This student team also sought to develop a testing program that trains new engineers in flight testing principles and will work to develop a testing site allowing for beyond line of sight UAV flight testing.
AeroVironment
Flight Demonstrations of Deployable Multirotor UAVs from the AV Puma LE
This student team attempted to take the hardware design developed from last year and progress it to a flight demonstration using cellular communications.
Airbus
Robotic Fuselage Inspection for Dents and Scratches
Before a fuselage is painted it needs to be inspected for dents and scratches. This is 100% manual today. This student team aimed to investigate a Vision/Laser system if it is on the market or invent a new one to be able to identify and capture images of any surface defamation. Additionally, this student team sought to investigate how a vision system detects defamation on the surface of a fuselage skin. The outcome this student team worked toward is thorough research on vision/laser technology related to fuselage inspection.
Airbus
Tactile Nosepiece Assembly
Many of Airbus Robotics' robots use nose pieces on drilling end effectors to normalize to the surface of a panel. This approach may be more robust and less expensive than their existing technology. This student team worked to build a functioning prototype of the device. This student team also worked to collect and assess data on the performance of a nose piece relative to a flat plate (Aluminum plate is okay) and to conduct research on technology necessary to improve the performance of the device -> resolution and range. This student team also sought to simulate the integration of the technology onto a drilling robotic end effector platform (Airbus Robotics provided details for the end effector).
Amazon
Customer Segmentation for B2B Fulfillment Services
Customer segmentation is the process of dividing the customer base into distinct and internally homogeneous groups in order to develop differentiated marketing strategies according to their characteristics. The customers Amazon focused on in this project were business shippers (e.g., book vendors), who ship bulk orders to businesses (e.g., book retailers). Amazon wanted to develop a systematic approach to find the optimal grouping of the customers and understand where they are in their respective lifecycle stages (e.g., onboarding, settled, mature, attriting). The goal was to use these information to prioritize Amazon's marketing/sales interventions and maximize the total customer lifetime value. This student team worked to create a tool that can take different sets of historical shipper demand data, historical intervention data, and resources cap data as input and generate optimal customer segmentation strategies (including customer size, lifecycle stages, and recommended treatments). This student team worked to produce, from the tool, intuitive visuals that work for marketing/sales teams.
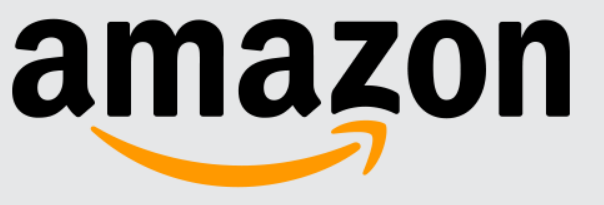
Amazon
Device Movement Detection
Amazon Lab126 is an American research and development and computer hardware company owned by Amazon.com. It was founded in 2004 by Gregg Zehr, previously Vice President of Hardware Engineering at Palm, and is based in Sunnyvale, California. Consumer radars are enabling wireless based sensing applications for smarthome. Certain radar applications rely on fixed device placement to function properly. For example, locating movements of subject with respect to the map of customer environment. Fixing the devices (i.e. wall mount) is not always an option. A method to detect the device has been moved and no longer "looking" at the same scene is required to notify user to take corrective actions. Otherwise, there will be missing data or false alarms that lead to poor customer experience. While this may be achievable with other sensors, there is a desire to minimize cost to solve this with radar itself. This student team sought to deliver a signal processing based software module that can output if the device has been moved out of its original position and orientation.
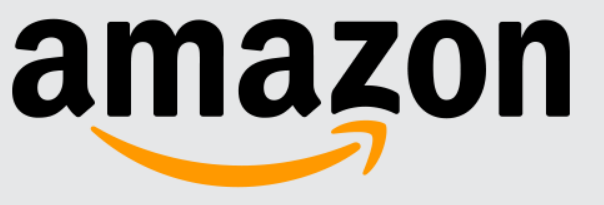
Amazon
IoT Position Application for In-home Robots
Amazon Lab126 is an American research and development and computer hardware company owned by Amazon.com. It was founded in 2004 by Gregg Zehr, previously Vice President of Hardware Engineering at Palm, and is based in Sunnyvale, California. With home robots (such as iRobot Roomba or Amazon Astro) becoming more commonplace in our households, there is potential to utilize their mobility and connectivity to solve problems in IoT localization. This enables use-cases such as finding lost devices and performing location-based actions on IoT devices. The main aim of the project is to predict the location of the IoT device using RSSI values that would be collected earlier during the radio map construction and route the robot to that location via the best possible route. This student team worked to develop a IoT localization algorithm that can locate an IoT device and reach to it via best route within an accuracy of +-10 cm. Moreover, the algorithm had to be generalizable to different homes and environments.
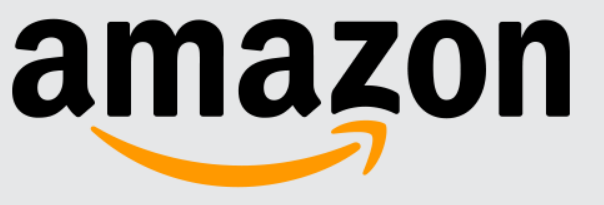
Amazon
Mixed Precision Block QR Implementation on GPU
Amazon Lab126 is an American research and development and computer hardware company owned by Amazon.com. It was founded in 2004 by Gregg Zehr, previously Vice President of Hardware Engineering at Palm, and is based in Sunnyvale, California. QR factorization is extremely powerful way to factorize a matrix into orthogoal matrix Q and upper triangle matrix R. One powerful use of it is in solving non linear systems. The drawback of this algorithm is compute complexity and thereby making it difficult to use for real time applications like robotics. This student team attempted to implement a fast version of this algorithm called mixed precision QR. In this implementation all matrix multiplication are performed in half precision and remaining operations like norm calculation and scalar calculations in single precision. Implementation used the GPU's half precision data type for the matrix multiplications and single precision for remaining operations. This student team worked to create mixed precision implementation of Tiled QR algorithms in Cpp running on x86 and mixed precision implementation of above on CUDA running on Nvidia GPU. This student team also sought to establish performance and accuracy results of the above mentioned implementations.
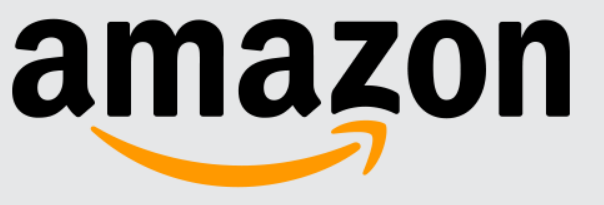
Amazon
Neural Architecture Design for Human Classification
Amazon Lab126 is an American research and development and computer hardware company owned by Amazon.com. It was founded in 2004 by Gregg Zehr, previously Vice President of Hardware Engineering at Palm, and is based in Sunnyvale, California. Deep neural networks trained on Imagenet like Resnet and MobileNetV2 are capable of detecting 1000 classes. However for practical usage, only a handful of classes are required to detect. For example for security cameras only human detection is required. This student team sought to find a network, including building a new model architecture, that shows best detection accuracy for detection of Humans. A key performance indicator was how much reduction of model size and compute measured in FLOPs. Advanced techniques for quantizing, clustering, and pruning (if used) would be a huge plus. Also performance numbers measured on edge device like Raspberry Pi would also be a plus.

AvtechTyee
Co-Cured Multi-Material Rod
AvTechTyee currently manufactures composite control rod and strut assemblies for aerospace applications. These products are typically manufactured from high modulus carbon fiber reinforced plastic (HM CFRP). Their current design includes a composite to metallic interface area, in which the carbon fiber material is in direct contact with titanium inserts. The conductivity of the metallic end fittings and the carbon fiber do not allow for electrical resistivity control in applications where that is a desirable property (i.e., lightning strike current guiding around fuel tanks). This student team worked to develop a co-cured multi-material composite rod to meet specific axial loading as well as electrical resistivity requirements. Initial thoughts are table rolled tubes using CF material at critical buckling and interface sections, and fiberglass or aramid fibers in non-critical sections to control resistivity. The outcomes this student team worked towards included: • Single or several standard design practices for interweaving multiple materials in single tube, including layup methods, interweaving geometries, curing profiles • Test data and reports – static/fatigue loading and resistive/lightning strike • Analysis methods for load and resistivity based on material and geometry inputs

AvtechTyee
Flight Crew Audio SoundSpace
The focus of this project was on the Flight Crew Audio Soundspace. This student team worked to create private sound fields at the Captain and First Officer nominal head positions capable of replacing the headsets normally worn by the flight crew during normal flight operations using networked microphones and ultrasonic drivers improving pilot comfort in a noisy environment. This is a targeted sound space and not the full cockpit. As an outcome of this project, this student team attempted to create hardware and software demonstrating stated performance.

AvtechTyee
Smart Design Database
AvTechTyee currently designs every new tie rod from scratch making every part of it unique. AvTechTyee currently uses a 50+ year old parts catalog to see if they have a similar rod that has been qualified and approved. This student team worked to create a smart database for which AvTechTyee would enter specific and critical parameters and get a return on if there is currently a rod that is similar. This student team also aimed to take these parameters and have the database output them into an Excel file that feeds into AvTechTyee's CAD and FEA packages to output models and simulations with little to no human intervention.
Blue Origin
Orbital Tube Welding EMI Simulation
Orbital Tube Welding (OTW) is a key operation in the assembly of space vehicles. OTW is an automated welding process in which the weld arc is rotated 360 degrees around the tubes that are to be joined, resulting in consistent and reliable welds. Performing welds on an integrated vehicle is avoided because the electromagnetic interference caused by the OTW equipment is a significant risk to avionics components on the vehicle. However, occasional welding near avionics components is necessary to accommodate late component arrivals or to replace a faulty line. This student team worked to simulate the electromagnetic interface caused by orbital tube welding to roughly gauge the risk of welding near avionics components. This student team worked to design, model, and build a demonstrator that includes a weld location, common avionics components, and locations for EMI sensors. This demonstrator is intended be used to analyze and validate a model of EMI at specific locations on a space vehicle as a result of orbital tube welding.
Related News
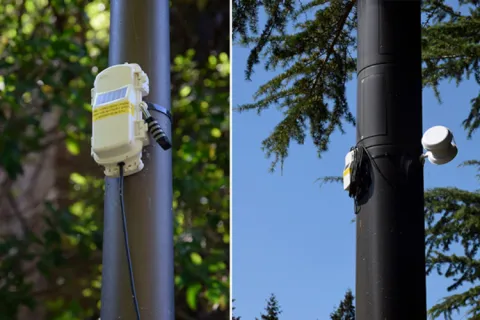
Fri, 09/20/2024 | UW Civil & Environmental Engineering
Smarter irrigation for a greener UW
A new project combines satellite data with ground sensors to conserve water and create a more sustainable campus environment.
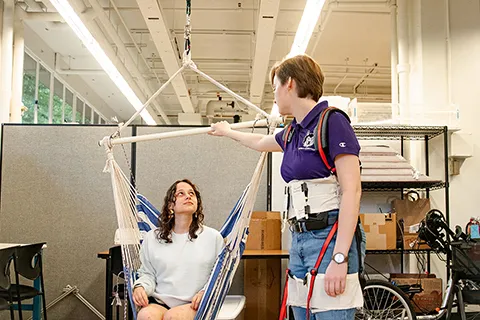
Mon, 09/09/2024 | UW Mechanical Engineering
Testing an in-home mobility system
Through innovative capstone projects, engineering students worked with community members on an adaptable mobility system.
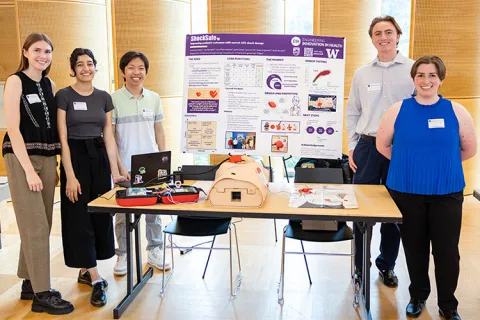
Mon, 08/19/2024 | UW Mechanical Engineering
Students strive to ensure accurate AED shock dosage
ShockSafe, developed by students with the help of mentors from Philips and Engineering Innovation in Health (EIH), can distinguish between children and adults during cardiac arrest emergencies.
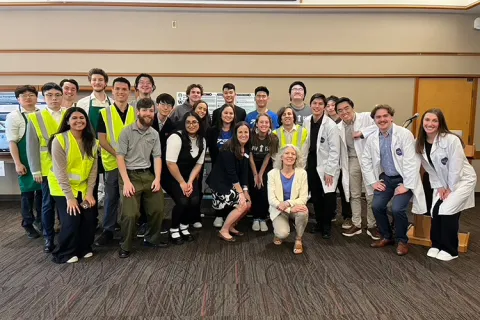
Wed, 08/07/2024 | Snohomish County News
Snohomish County, University of Washington partnership boosts efficiency in enterprise scanning center
UW Industrial and Systems Engineering Capstone Project set to save Snohomish County over $40,000 annually.