Industry-Sponsored Student Capstone Projects
2022/2023
In the 2022/23 academic year the industry capstone program was supported by 56 sponsors and 99 real-world projects. Nearly five hundred and fifty students from across the College of Engineering participated. Scroll down to learn more about each project.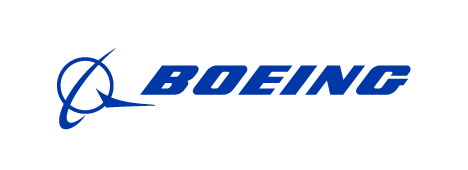
Boeing
Additive Manufacturing Data Analytics, Computational Material Modeling
Additive manufacturing (AM) is a digital process that provides critical information across the entire process lifecycle from product definition, manufacturing, test/inspection and final acceptance. This information is comprised of large spatial and temporal data sets that provide insights to the quality of the final manufactured part. These data sets currently reside on disparate systems which can limit correlation and advance AM process understanding and insights This student team worked to integrate these data sets into a "super set" of data that is registered and fuse together using data consolidation and visualization techniques. With the data integrated, this student team would then attempt to apply new computational material science techniques to infer relationship between in process, post process, and material microstructure data. The models, upon validation, could be used to predict material microstructure and resulting part performance based on process parameters and geometric data. The desired outcome this student team worked to accomplish was novel computational material models applied to existing UW data sets through the development of new software packages that enable process to microstructure correlations. This project would be a complementary addition to the UW round robin study, by providing further guidance and funding on the data analytics scope of work.
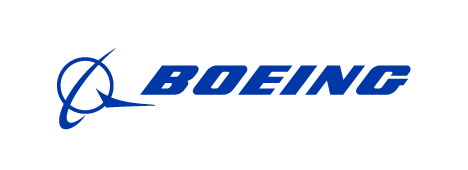
Boeing
AM Machine Gas Flow Characterization & Improvements
Gas flow in the metal AM printers is a key process variable. Recirculation and non-uniformity of the gas flow in the printer can be a source of material defects. Using the a mock-up of the EOSM290 printer built by the 2022 capstone team, this student team worked to design & build gas flow devices to reduce the recirculation and non-uniformity within the printer and test them, using Particle Image Velocimetry (PIV) to characterize the improvements. Students also worked to print and fatigue testing material to demonstrate the impact of gas flow improvements or different gas flow settings. The outcome this student team worked towards is to generate PIV analysis of the baseline gas flow in an EOSM290 printer, design devices to improve the gas flow, and generate PIV analysis of the improvements. Students also worked to analyze materials printed with the improvements and/or different gas flow settings to demonstrate the impact on material properties (fatigue) from gas flow.
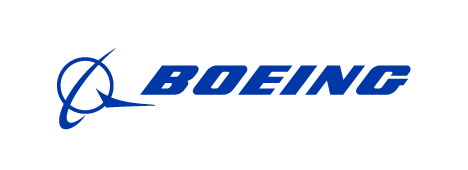
Boeing
AM Tooling & Internal Structures
Previous FSAE aerodynamic wings were manufactured using traditional machined foam and polymer features to create a defined shape. With these types of tools the internal structure has to be removed after cure, and once removed are left with a hollow structure. A slit is placed on the rear facing edge to allow access for the internal supporting structure to be installed. The traditional method consists of multiple steps, and this capstone hopes to reduce these steps. This project was meant to assist in the students learning about additively manufactured (AM) tooling and topology optimization structures within a composite aerodynamic wing. The AM sub-structure could be used for multiple purposes; to support in tooling for composite layup, curing of the composite wing, and structure to support on the car. The process aimed to help reduce manufacturing time and create an opportunity for students to understand the interaction between composites and polymers.
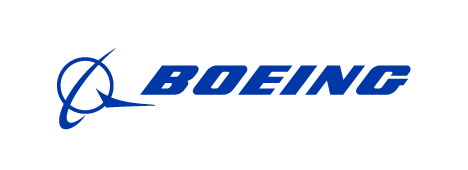
Boeing
Analyzing Airplane System and Security Logs for Context Awareness
Modern e-Enabled Airplanes and Ground Support systems and their associated sub-systems produce high volumes of log data. How can Boeing better automate and conduct data extraction relating to a sequence events, and automate identification and add context to the analysis of anomalous cyber events in operator airplane log files? Project outcomes this student team worked toward include: • Concept of operations and initial systems description • Trade study plan to iterate to best configuration • Development of Context Aware prototype to enhance Airplane Security Log File event profiles and analysis. Interim deliverables this student team worked toward include: • Bi-weekly meetings on progress and lessons learned • Preliminary Design Review material Final Deliverables • Final technical report which shall present the design of the Context Aware system clearly and concisely; it shall cover all relevant aspects, features, and disciplines. Pertinent analyses and studies supporting design choices shall be documented.
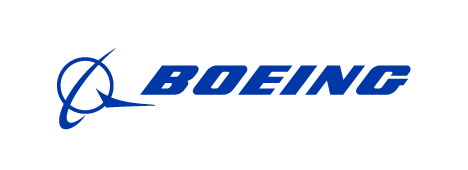
Boeing
Boeing Facilities Service Requests
Boeing Facilities is responsible for responding to Service Requests across all Boeing sites, ranging from production critical equipment repairs to routine custodial requests. Requests are received through the front-end Service Request form, then must be routed to the correct team's back-end Work Order queue to assign the work. Any mistakes made through the form can cause significant delays to the fulfillment of the Service Request. This student team worked to revise the form to reduce the error rate and ensure Service Requests are directed to the correct team. To work toward this goal, this student team sought to analyze historical Service Request data, interview key stakeholders, and design an improved front-end Service Request form. The student team worked to perform statistical analysis on the Service Request data set to identify high-error areas and will seek to develop visual tools for tracking and reducing the error rate. Using this analysis, the student team attempted to develop targeted improvements to the Service Request form to reduce errors. Anticipated outcomes this student team worked towards for this project included: - Determine the current error rate for 1 week of data, re-calculate error rate after implementing short term error proofing/improvements - Develop visual tools for data analysis of Service Requests - Analyze current form and suggest short term error-proofing/improvements - Interview stakeholders to determine correct information needed from customers - Provide a re design concept for the Facilities Request Form
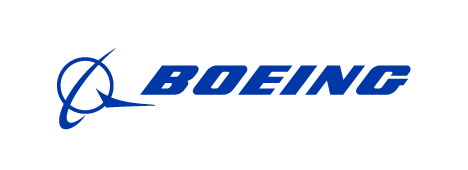
Boeing
Boeing Regional Utility Freighter Aircraft
Air cargo remains a key element of global trade carrying 35% of total trade measured by dollar value. However, one potentially under-served area is easily moving freight to and from the more outlying areas to the larger cargo hub airports. These areas would traditionally be served by small cargo aircraft or by road trucks, where cargo needs to be unpacked and repacked for the smaller transport. Particularly in a pandemic environment, this slows down distribution of critical supplies and perishable goods to and from outlying areas quickly and efficiently. This student team sought to build a freighter aircraft that can carry main deck ULDs and/or pallets, that are used on 777 / 767 / 747 /A330 / DC-10 / MD-11 aircraft. The student team also worked towards identifying how to use Sustainable Aviation Fuel and to be loaded and unloaded at smaller airports, with limited ground handling loading equipment. The intended outcome of the project was an aircraft design that meets the requirements and is validated through limited testing. To meet this outcome, the student team worked to produce a technical report that presents the design of this aircraft clearly and concisely, including all relevant aspects; The student team endeavored to provide pertinent analyses and studies supporting design choices, to create a scale wind-tunnel model, and to provide experimental results from the wind-tunnel test.
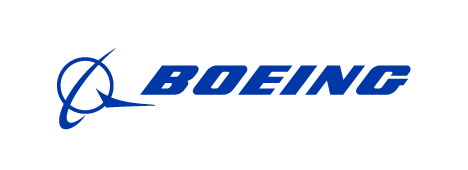
Boeing
Carbon Fiber Tube Space Frame
The project team attempted to design joints for a carbon fiber tube space frames. For a steel tube space frame a triangulated joint is welded together, however with carbon fiber, welding is not possible. We proposed making metal joints where the carbon fiber tubes can slide into the joint and be bolted together. Using the bolts, we could still attempt to use perimeter shear data and tearout calculations.
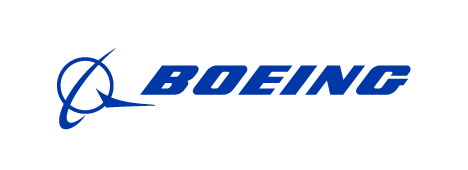
Boeing
Lightning Strike Effects on Full Depth Scarf Repairs
Full depth scarf repairs on composite structure introduce a slightly different stack up that might alter the Electro Magnetic Effects (EME) from the original design. Predicting the outcome of a lightning strike attachment to a scarf repair will be helpful to understanding if the repair patch will resist the lightning strike energy from penetrating the thickness of the repair patch. This student team sought to characterize the performance of scarf repairs subjected to lightning strikes of significant intensity (100-200 kA). This student team worked to install scarf repairs on a representative fuselage panel and evaluate various protection schemes/shields installed on the inside/inner mold line (IML) of those panels for effectiveness. Outcomes this student team worked towards included: 1. Test results of lightning strike effects on scarf repair areas. Evaluation of mitigating protection schemes. 2. Publish conclusions and recommendations of testing.
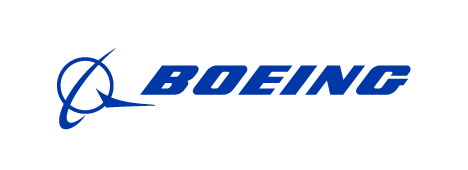
Boeing
MBSE Threat Trees
This student team sought to create a framework for cybersecurity Threat Trees (Attack Trees) in the Boeing MBSE Environment. The framework related the Threat Trees to SysML model elements such as Fault Tree objects, structural blocks, and system behavior (which will be provided by Boeing). The Threat Trees aimed to establish qualitative ranges, in rough quantitative terms, to help determine likelihoods and assurance levels. The intended outcomes for this project included: 1) Identify and customize a graphical front-end a. Used to create Threat Trees for Cyber-Physical avionics systems, needs to be simple and flexible b. Create custom Threat Tree symbols and add Properties to support the framework c. Properties must support rough quantitative assessments using basic risk assessment methods d. Properties must support integration of Security Assessment with Safety Analyses (fault trees) 2) Create Cameo macro (Python) to parse the Threat Trees (which are presumably exported to xml) and build Cameo Generic Tables containing Threat Tree objects to be used in the framework 3) Create the Risk Assessment framework for threat tree objects in SysML and Python. The framework must be capable of relating threat conditions to system hazards and fault tree elements, see RTCA DO-356. There is some design freedom, but the framework should be adaptable to various avionics systems, and is expected to include proper SysML relationships, SysML diagrams, and Cameo dependency matrices. 4) Create a demonstration project which uses the framework. The demo should be based on a simple aircraft function which uses an ARINC 664 network. The demonstration must show end-to-end capabilities of the framework (threat tree creation to system hazards, structure, and fault trees). 5) Present the demonstration and project summary to Boeing Cybersecurity team members, ARINC 664 network team members, Avionics team members, Boeing Fellows, and associated managers.
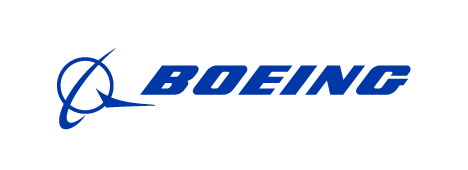
Boeing
Mechanical Fixture for Surface Treatment Process Control
This project provided students an opportunity to learn more about mechanical design, system fabrication, automation, surface preparation of thermoplastics, and structural repair of composites. The hope was that students would have an opportunity to gain some hands-on experience on system design, build, and implementation. This student team worked to advance and improve on a mechanical fixture /guidance system for use with the different commercially available portable options for surface treatment of thermoplastics (plasma/laser/UV light) to achieve the following: 1. Accurately control prescribed pass speeds for all options 2. Guided consistent overlap between passes 3. Maintain constant, controllable nozzle distance from substrate 4. Variable clamping mechanism for different nozzle sizes 5. Minimum 3-axis numeric control 6. Clamping system with vacuum suction cups to ensure secure completion of surface treatment coverage Anticipated deliverables for this project included: 1. Report, including any design(s), prototype(s), and/or simulation(s) developed during the effort. 2. Mechanical proof of concept demonstration, if feasible.
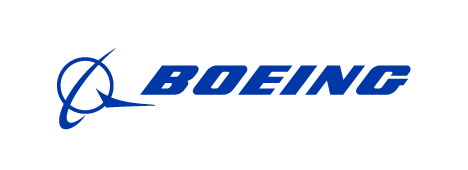
Boeing
Methods for Analyzing Synthetic Fuels Onboard for Data Collection and Indication
Boeing has committed to have aircraft compatible with Sustainable Aviation Fuel (SAF) by 2030. We need to consider that in operation, we will have a mix of both fossil based and synthetic fuels in our fuel tanks, with no external ability to know what percentage of the mixture will be of both fuel types. We also need to consider that any power or electric current in a fuel tank poses a risk of ignition and should be removed from the tank. The student team on this project worked to develop different unique and novel methods or technology that do not utilize electrical power internal to a fuel tank to measure different fuel properties. For this project, we assumed that the synthetic fuel has the bounded properties as specified in ASTM D7566 Annex 2 (HEFA), and that fossil based fuels has properties as specified in Table 1 of ASTM D1655. The student team worked to develop methods of analyzing the fuel using no electric current and reporting the following properties: • Density • Dielectric Constant • Fuel height • Hydrocarbons measurement (CnH2n) Note current Fuel Quantity Indication Systems (FQIS) use both capacitance and sound to measure fuel height and should not be considered as part of this study. Anticipated outcomes of this project included the identification of methods of measurement and analysis of a mixture at any ratio of Fossil based and Synthetic fuels and to consider estimates of the following criteria: • Weight • Materials • Safety • Cost • Feasibility • Risks • Application of data collected (Value) – Ideas of how this data could be used to add value to a customer • Accuracy The student team on this project aimed to present the idea(s), considerations, and how the above criteria was evaluated. Level of detail is expected to be at Technology Readiness Level (TRL) 2 – Technology Formulation (Concept and application have been formulated).
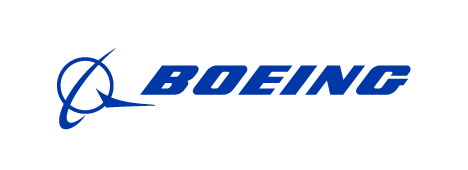
Boeing
Optimized Gooseneck Hinge
This student team aimed to design, analyze, fabricate (using selected aerospace grade material) and test a goose neck hinge component in tension and compression using the UW ME load test frame. Any successfully tested hinge component is to be provided to Boeing at the conclusion of testing for further evaluation. The hinge has unique envelope requirements to fit in available space. A large portion of the exercise was to select a material and fabrication technology that would both meet the prescribed requirements, and be tested within the allotted time frame and project budget. Aluminum, steel, titanium, CFRP may be selected. This hinge design is similar to the DC-9 passenger entry door hinge.
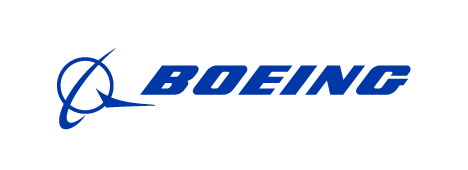
Boeing
Part Smoothing Models for Additive Manufactured Titanium
Additive Manufacturing (AM) is quickly transforming industrial manufacturing with the ability to produce high strength, low weight parts with intricate designs that are too complex to manufacture by conventional methods. However, the finishing/smoothing (post processing) of parts remains one of the biggest challenges for enabling full and affordable implementation of AM. This student team sought to create a model that accounts for reaction kinetics, gas, and fluid flow and how it interacts with intricate part shape to design an optimal chemical processing configuration on internal surfaces. This student team worked to include documentation on how the model was created, with attention to the underlying assumptions that were made and known limitations, as well as a copy of the final model (to include examples of how it is used, if built using common software).
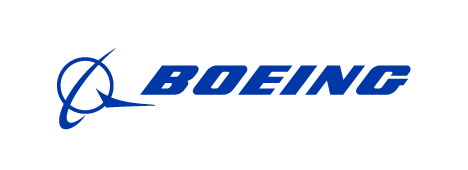
Boeing
PBF Build Process Interruption Study - Phase 2 Fatigue Study
The existing UW Round Robin focuses on EOS M290 intra-build, intra-machine, and inter-machine variation study in both static and fatigue material behavior. The study is supported by industrial members and FAA. With the project progress in 2020 and 2021, there are ideas about where these variations may come from. With the existing UW Round Robin study transition into fatigue focus and literature studies, performance variation exists and many studies are in place to further understand the variation sources. Besides typical process parameter studies, the effects on the process/ machine induced build variation is yet to be well understood. By using Round Robin data, it greatly reduces the amount of preparation and design of experiment time, allowing students to focus on one of the key interests in variation factor. The data received from the interruptions study will continue to support production non-conformance decision. This student team worked to leverage the existing DoE design in Round Robin study and design interruptions in the build process and study its material behavior tolerance on various interruptions. Anticipated deliverables included: • For the interruption design, this student team will work to design interruption locations and degreed of the interruptions • This student team will work to identify effects on fatigue performance for machined coupons with and without HIP • This student team will work to create documentation on the surface variations in as printed condition • This student team will work to understand defect characterization via NDE such as SEM and Micro-CT
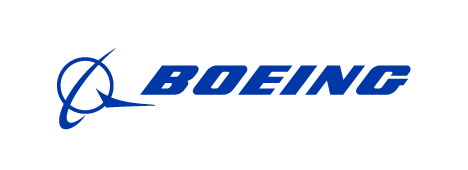
Boeing
Photopolymer Additive Manufacturing UV Stability
Additive Manufacturing (AM) is revolutionizing the way Boeing fabricates aerospace components by enabling increasingly complex part designs. The Photopolymer 3D printing process has many advantages including the ability to print small complex parts with excellent surface finish. Historically the use of photopolymers in aerospace production have been limited by poor elevated temperature mechanical properties, flammability, and susceptibility to ultraviolet (UV) degradation. Recent advances in photopolymer materials have improved temperature resistance and flammability, but the material remain susceptible to degradation when exposed to UV light. Aerospace parts may be exposed to UV light during manufacturing, storage, and while in-service, so understanding the material degradation and ensuring adequate protection is crucial. This student team worked to focus on evaluating coating technologies to shield photopolymer parts from UV light and studying the UV degradation of AM Photopolymers. This student team also worked to gain experience applying their classroom knowledge to a real-world problem with no predetermined “right answer.” Through collaboration on a cross-functional team, this student team attempted to execute this ambitious project and gain insights on what it is like to work at a company like Boeing.
Related News
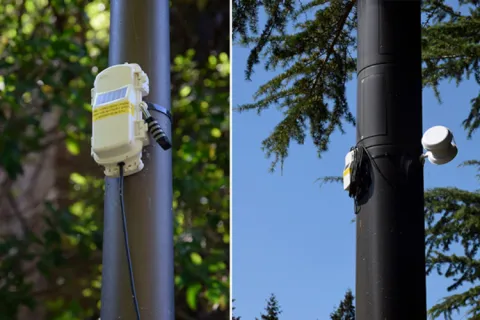
Fri, 09/20/2024 | UW Civil & Environmental Engineering
Smarter irrigation for a greener UW
A new project combines satellite data with ground sensors to conserve water and create a more sustainable campus environment.
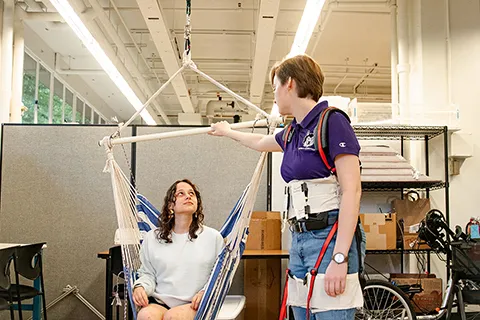
Mon, 09/09/2024 | UW Mechanical Engineering
Testing an in-home mobility system
Through innovative capstone projects, engineering students worked with community members on an adaptable mobility system.
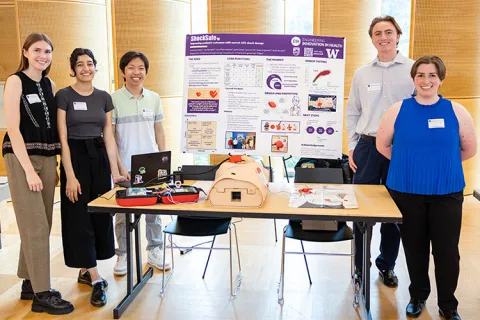
Mon, 08/19/2024 | UW Mechanical Engineering
Students strive to ensure accurate AED shock dosage
ShockSafe, developed by students with the help of mentors from Philips and Engineering Innovation in Health (EIH), can distinguish between children and adults during cardiac arrest emergencies.
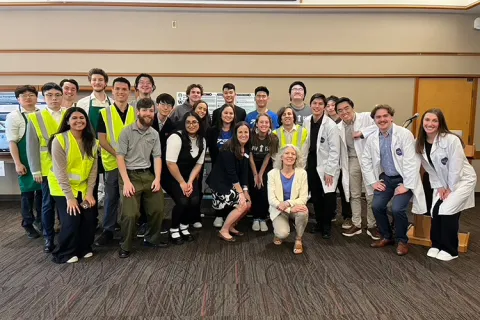
Wed, 08/07/2024 | Snohomish County News
Snohomish County, University of Washington partnership boosts efficiency in enterprise scanning center
UW Industrial and Systems Engineering Capstone Project set to save Snohomish County over $40,000 annually.