By Chelsea Yates / Photos by University of Washington
October 28, 2019
ME’s new titanium 3D printer is the only one of its kind at the UW and one of just a few at universities nationwide.
ME’s newest 3D printing lab explores additive manufacturing of complex structures with titanium.
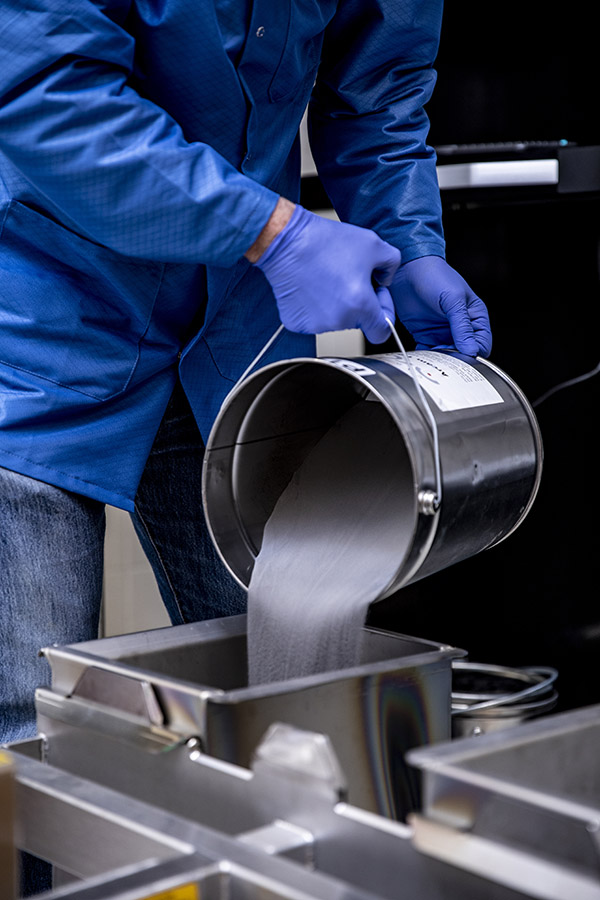
The 3D printer uses titanium powder, which is dispensed in layers and consolidated to create a solid object. Leftover powder is collected and reused to reduce waste.
3D printers can print objects from a variety of materials: plastics, ceramics, glass, nylon, resins, even chocolate. Thanks to recent advancements in additive manufacturing technology, engineers can add titanium to this list. An earth abundant metal, titanium is valued for its unique mechanical properties and high strength-to-weight ratio.
However, due to its strength and high melting point, titanium is difficult to convert from its raw form to a finished part. This makes manufacturing processes challenging and uneconomical, and it limits the applications of the metal. But engineers hope that advancements in 3D printing will change that.
“Titanium 3D printing has the potential to open new pathways in additive manufacturing for industries ranging from health to aerospace,” says ME professor Ramulu Mamidala, who leads the Metal 3D Printing Lab as part of the Washington state-funded JCDREAM (Joint Center for Deployment and Research in Earth Abundant Materials) initiative. “It’s really about discovering the art of the possible.”
In 2017, the lab acquired a 3D printer capable of printing titanium. It’s the only one of its kind at the UW and one of just a few at universities across the country.
The print area is prepared for the printing process, which involves selective powder bed fusion technology using a high energy electron beam.
Titanium 3D printing: Why and how?
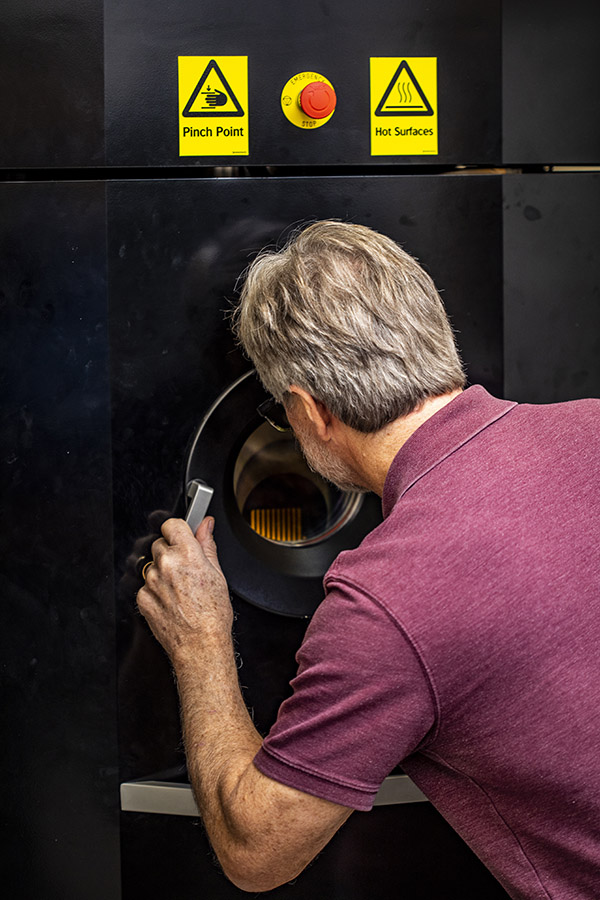
ME lab engineer Bill Kuykendall checks the status of a print job. Printing takes place inside a vacuum chamber, where temperatures reach up to 1600 degrees Celsius and the titanium easily melts.
There are several benefits to printing titanium. In addition to being abundant and strong, it is corrosion resistant and melts at a much higher temperature than most common metals. It’s also lightweight and biocompatible, making it a very good material for surgical implants and medical devices.
“3D printing titanium can result in excellent mechanical properties if ‘correct’ process parameters are used,” says Rishi Pahuja. He served as the lab’s primary research scientist last year while completing his mechanical engineering PhD.
“Our team is focused on studying the effect of these parameters on mechanical properties,” he adds. “We can attain precision and complexity in design that traditional 3D printing machines are not capable of achieving.”
ME’s titanium 3D printer uses selective powder bed fusion technology and a high energy electron beam in a process that generally takes place over two days. A 3D computer model is created by researchers, uploaded to the printer’s software and sliced into layers in preparation for the print. The printing takes place inside a vacuum chamber, where temperatures reach between 700 and 1600 degrees Celsius and titanium melts and flows easily. Titanium powder is dispensed in layers, and the electron beam fuses and consolidates each layer to the one before it, welding together hundreds of thousands of tiny particles of powder. Layer upon layer, a solid object is created and embedded within a block of powder.
Inside the chamber, an electron beam fuses layers of titanium powder together. Eventually, a solid object is created and embedded within a block of powder.
Once the print is finished and has cooled, the block is removed and the parts are extracted. Lab engineers collect and reuse the leftover powder to reduce waste and expenses. According to Mamidala, unlike conventional machining processes, where over 80% of the raw material is cut away and wasted, this process wastes less than 5%.
The researchers say this printing method is more versatile than traditional manufacturing methods, and because of how easily parts can be designed and printed, complex geometric forms can be easily created, allowing for more efficient prototyping and part testing.
Advancing possibilities
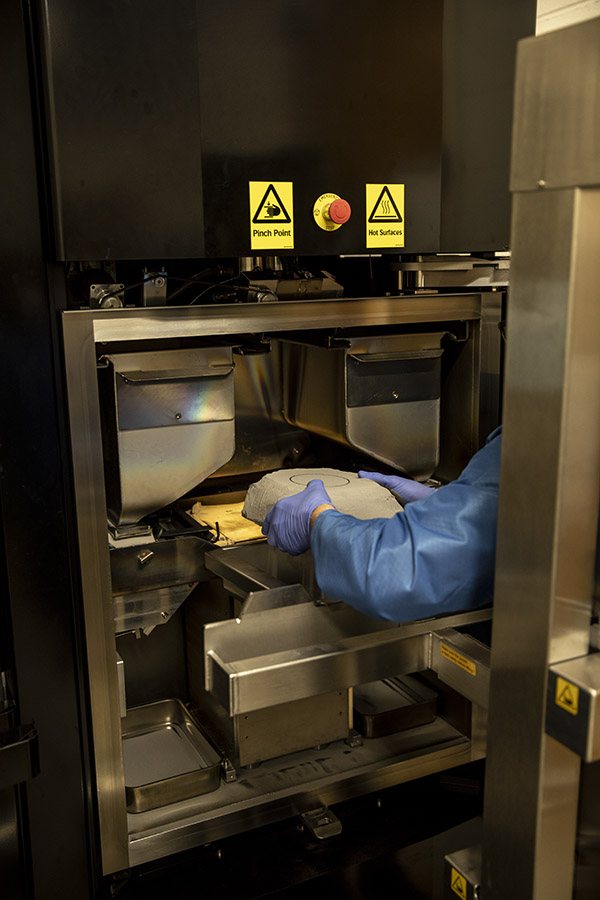
Once the print has finished and cooled, the powder block is removed and transferred to a separate station where the object is extracted from it.
From energy to transportation, many major industries currently depend on rare earth materials as well as materials mined using unsustainable practices. According to JCDREAM, heavy reliance on rare earth minerals and conflict resources has stifled U.S. industry growth. Through collaborative research, development, education and leadership the center hopes to make Washington state a leader in developing advanced, clean energy-focused manufacturing practices.
Mamidala sees titanium 3D printing technology development as a key way to do this.
“The more we can develop ways to use more earth-abundant materials like titanium in manufacturing, the more we can reduce our dependence on rare and unsustainable materials,” he explains.
He adds that it’s especially important for universities like the UW to be involved in this work.
“Titanium 3D printing is going to revolutionize industries where lightweight, complex geometries are essential to a design’s performance,” he says. “Additive manufacturing places us on the cusp of enabling the next major changes in aircraft and spacecraft capability; therefore, UW engineers with this experience will be in high demand worldwide as 3D printing continues to change how manufacturing occurs.”
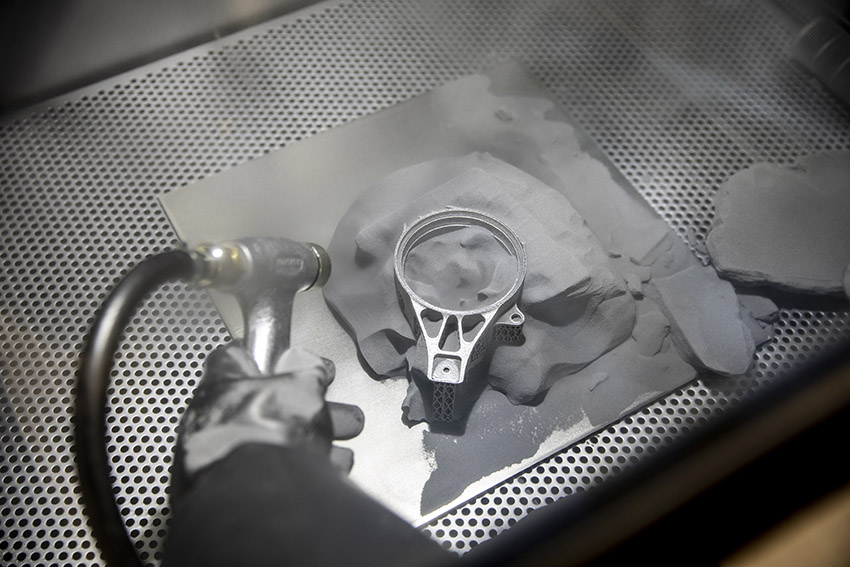
As the powder is blasted away, the solid object — a wheel hub mount — begins to appear.
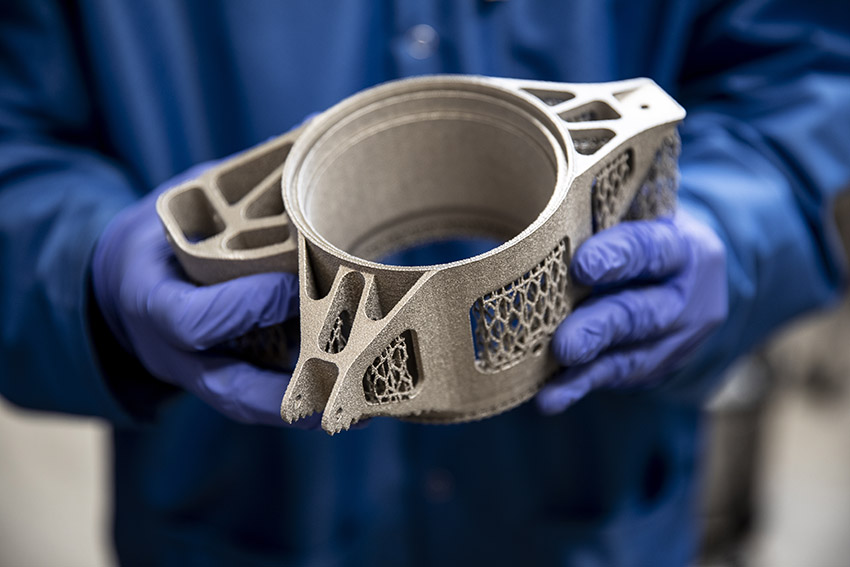
The finished wheel hub mount. Notice the intricate details. Titanium 3D printers are capable of creating complex geometric forms more so than traditional manufacturing methods.
Kuykendall, left, and research scientist Rishi Pahuja (ME PhD ’19), right, compare the finished product to their original computer model.
The Metal 3D Printing Lab is interested in exploring project ideas with the UW community. Lab engineers have already been working with the Boeing Advanced Research Center on several student capstone and test projects to replace multi-piece machine-made airplane parts with a single titanium part. They are also partnering with materials science and engineering researchers to determine how many times titanium powder can be recycled and with bioengineering researchers to develop the design of printed bone implants.
“3D printing titanium is going to revolutionize industries where lightweight, complex geometries are essential to a design’s performance,” says ME professor Ramulu Mamidala, center.
“Already, the printer is allowing us to realize and produce organic shapes inspired by natural structures that could only previously be imagined,” Mamidala says. “This technology further drives the creative side of engineering to solve problems in new ways and in this way it’s really bringing art, science and engineering together.”
Learn more about the Metal 3D Printing Lab. Those interested in collaborating on a project can contact Ramulu Mamidala at ramulum@uw.edu.